A talented aerospace engineer with a passion for lightweight construction, Thomas Spoida worked in racing before moving on to corporate research for an auto manufacturing company that welcomed his ideas on new materials and technology. Unfortunately, though, change was often too costly to implement.
Undaunted, Spoida devoted himself to researching ways to make constructing lightweight components more affordable. Eventually the solution was clear — clever topology optimization and subdivisions, which he achieved using a combination of ZBrush and CAD.
How did you figure out that 3D software could be used as part of the process?
Spoida: First, I want to explain that topology optimizations mostly generate very organic shapes, so think of it as something like how nature makes a tree grow. There are no right angles or sharp edges. To turn a topology optimization result into a real part, the output has to be reconstructed in CAD.
Normally, that is done with parametric solid modeling in CAD, but that only allows the organic shapes from the optimization to be reproduced to a very limited extent, and you don’t get the lightest component possible.
Today, subdivision modeling is integrated into all CAD tools and is usually advertised as a design and styling feature but, in our experience, they’re not as fast and powerful as 3D modeling tools designed for that purpose, and they have no sculpting functionality.
Generally, we work no differently than artists using 3D tools for gaming and films. In our case, though, the topology optimization result must first be interpreted. In most cases, many holes have to be closed because they can cause problems in the casting process. Certain demolding angles also have to be set so the part can be removed from the casting or forging mold later.
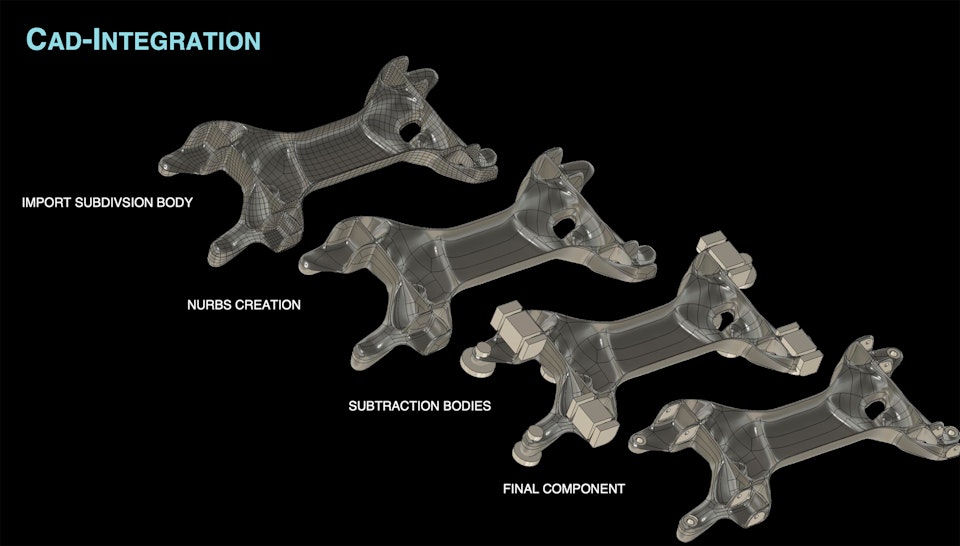
We do all of that high-poly modeling in ZBrush using a variety of sculpting brushes, and we learned about that in 2019 when my employer at the time allowed us to fly to Los Angeles and to meet with Pixologic. We spent two very intense days with Ofer Alon, Jaime Labelle, Joseph Drust and Paul Gaboury to talk about the use of ZBrush in engineering.
As a result, the guys implemented two features we needed in a very short time, which was definitely a gamechanger for us. In the end, it's always about getting the polycount as low as possible, because we want to import the subdivisions into CAD and allow our customers to adjust them in the CAD subdivision modeling tools.
Comments
Add comment