Say more about how subdivisions make it possible to have a continuous process from optimization to production.
Spoida: The complete development cycle is now based on meshes. Using subdivision modeling, we can generate the so-called design space within a very short time. This means we fill the available design space for the part to be optimized. This can be done very comfortably with ZBrush, and we can be sure that we have really used the last corner to get the lightest possible part from the optimization.
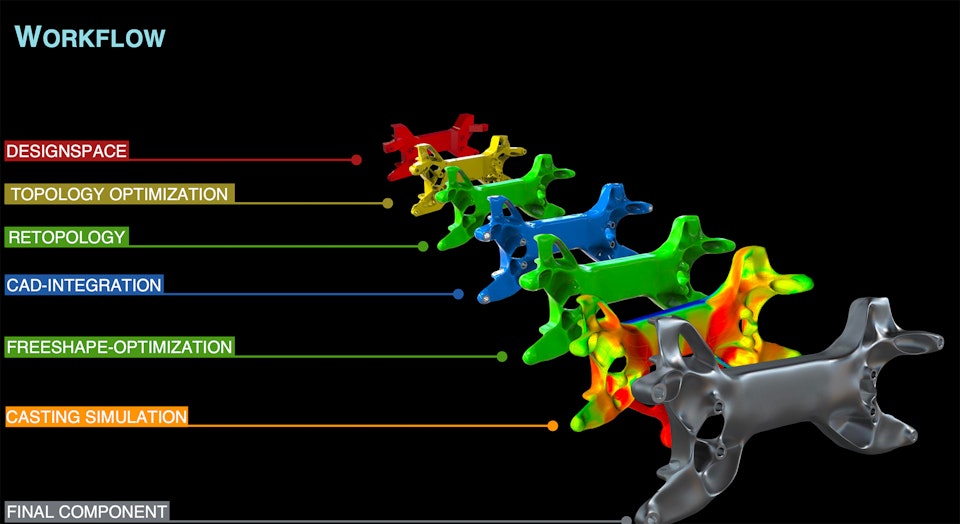
The simulation, or optimization, is also done on meshes, which are not polygon meshes, but can be derived from them. After the design phase, we move on to manufacturing the components. In addition to casting, forging also plays a major role. The supplier forging the component receives the final geometry of what we call the “blank,” or the geometry that falls from the forge before machining by milling.
Forging is not done in one step. It starts with a thick, round metal cylinder, which becomes the final component in several forging processes. The geometries of those intermediate steps normally have to be designed in CAD at great expense, but subdivision modeling makes the process much faster and more precise. In the simplest case, the SubD body is simply adapted to the final geometry without changing the topology.
What effect is this new type of subdivision modeling having on the manufacturing, particularly the automotive industry.
Spoida: 3D modeling tools like ZBrush can be used to model mechanical parts in an extremely short time and, to date, lightweighting has not played a role in the automotive industry. Thanks to topology optimization and the implementation of subdivisions, we are now able to develop extremely lightweight components for normal mass production processes, such as casting and forging.
Depending on the manufacturing process we are using either sculpting in combination with ZRemesher or we retopologize the topology directly with ZModeler.
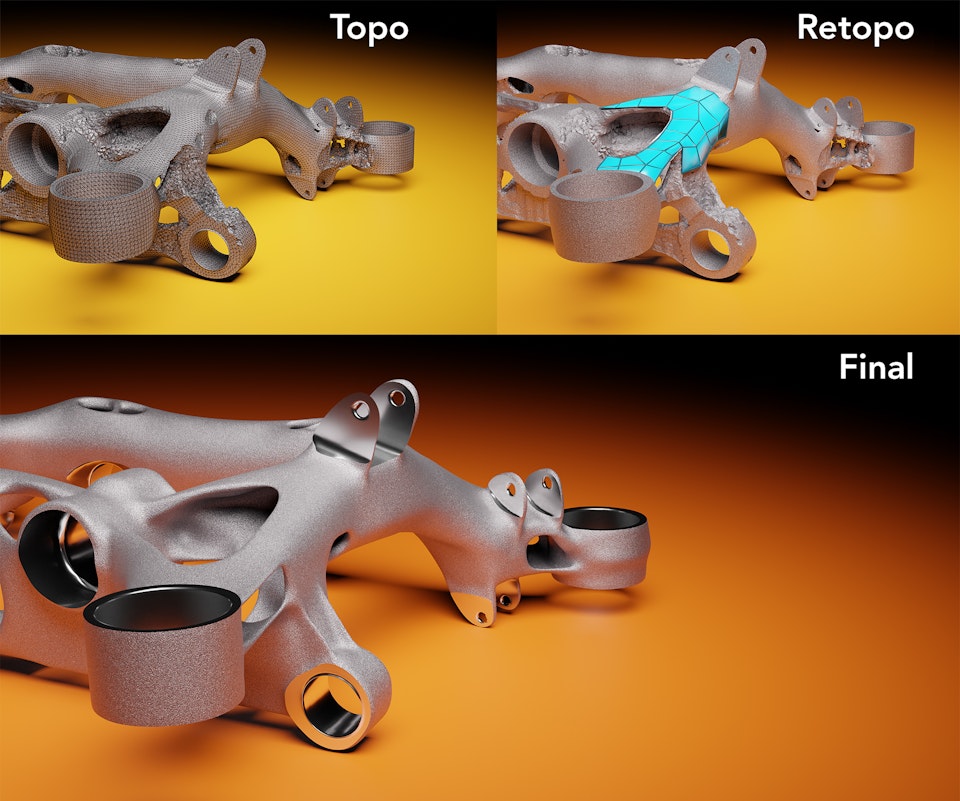
This is beneficial for a lot of reasons. Lightweight components require less material, so they save money. If we have to optimize a cast component, for example, we do not change the manufacturing process, we just reduce the material input as much as possible and that’s reflected in the component costs.
In recent years, the topic of electromobility has become increasingly important and is now gaining momentum. But electric cars have challenges that combustion vehicles don’t, particularly the issue of range. Logically, the heavier the vehicle, the greater the mass that has to be accelerated, which has a direct impact on range.
Batteries are the main factor determining range, but they are very heavy and you can't install batteries of any size to get more range. That’s why it’s even more important to make the rest of the vehicle’s structure as light as possible. And lighter vehicles help save precious energy and are more sustainable over time.
How does Bionic Mesh Design work with customers?
Spoida: In most cases, we provide the full service from generating the design space, topology optimization and retopology until CAD integration. In some cases, though, customers hand over a topology optimization result that we just have to retopologize.
Automotive plays a major role for us, but for all other industries where transport plays a role could benefit from lightweighting, like naval industries and aerospace.
Comments
Add comment